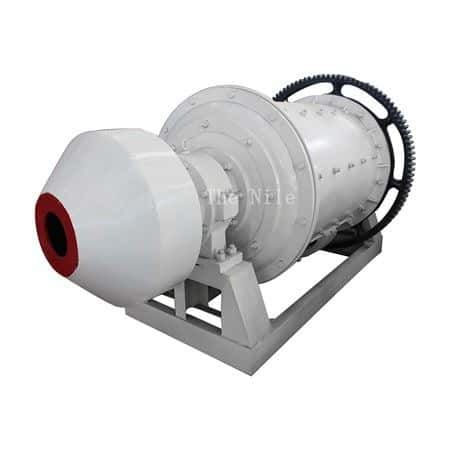
Applied Field: High energy ball milling plant is mainly used for dry and wet grinding for chrome, gold, tin, coltan, tantalite, silica sand, lead, and pebble. High energy ball milling machine is widely applied in building material, refractory material, fertilizer, ceramics, glass, and other industries.
Working Principle of High Energy Ball Milling
The material enters the first bin of the high energy ball milling machine evenly by the feeding device through the feeding hollow shaft. There are stepped lining plates or corrugated lining plates in the bin, of high energy ball milling, which is filled with steel balls of different specifications. The centrifugal force generated by the cylinder rotation will bring the steel ball to a certain height and then fall down, which will have a heavy impact and grinding effect on the material. After coarse grinding in the first bin, the material enters the second bin of high energy ball milling plant through the single-layer partition board. The bin is inlaid with a flat-lining plate with steel balls to grind the material further. The powder is discharged through the discharge grate plate to complete the grinding operation of the high energy ball milling machine.
Tips for Purchasing High Energy Ball Milling
1.Ensure the production capacity of the high energy ball milling machine. The selected grinding equipment can achieve the required output under the condition of achieving the required grinding fineness.
2.The production capacity of high energy ball milling machine should be higher than designed. The change of ore hardness and fineness should be considered in the design. Generally, the ore in the deep part of the ore deposit becomes hard or thin, the selected grinding mill should also be able to adapt to ensure the smooth operation in the initial stage.
3.Grinding test must be done. Grinding test must be done. When there is no actual data in the design, grinding test must be required. Especially for large-scale concentrators, the grinding machine selection calculation, and scaling from the basic data obtained.
4.Proper consideration should be given to large-scale equipment.Due to the large-scale equipment, the overall high energy ball milling machine is lighter in weight, less occupied area, less production system, fewer operators and auxiliary systems, and low corresponding investment and production costs.
5.However, the requirements of operation and management level of large-scale high energy ball milling machines are high. If the operation rate of ball mill machine is slightly reduced, the output of the concentrator will be greatly reduced.
Model | Ball loading (t) | Feed size(мм) | Size | Performance engine power (kw) | Weight |
Ф900×1800 | 1.4 | ≤20 | 0.075-0.89 | 18.5 | 3.6 |
Ф900×2100 | 1.7 | ≤15 | 0.075-0.83 | 15 | 3.9 |
Ф900×3000 | 2.7 | ≤20 | 0.075-0.89 | 22 | 4.5 |
Ф1200×2400 | 3.5 | ≤25 | 0.075-0.6 | 30 | 11.5 |
Ф1200×2800 | 6.8 | ≤25 | 0.075-0.6 | 37 | 13 |
Ф1200×4500 | 5.5 | ≤25 | 0.074-0.4 | 55 | 13.8 |
Ф1500×3000 | 6.8 | ≤25 | 0.074-0.4 | 75 | 17 |
Ф1500×4500 | 10.5 | ≤25 | 0.074-0.4 | 110 | 21 |
Ф1500×5700 | 15 | ≤25 | 0.074-0.4 | 130 | 24.7 |
Ф1830×3000 | 13 | ≤25 | 0.074-0.4 | 160 | 28 |
Ф1830×3600 | 15 | ≤25 | 0.075-0.4 | 160 | 33.5 |
Ф1830×4500 | 17 | ≤25 | 0.075-0.6 | 185 | 35 |
Ф1830×7000 | 25 | ≤25 | 0.074-0.4 | 210 | 36 |
Ф2100×3600 | 21 | ≤25 | 0.074-0.4 | 185 | 46.8 |
Ф2200×5500 | 30 | ≤25 | 0.074-0.4 | 245 | 48.5 |
Ф2200×6500 | 35 | ≤25 | 0.074-0.4 | 380 | 52.8 |
Ф2200×7500 | 33 | ≤25 | 0.074-0.4 | 380 | 56 |
Ф2400×3000 | 30 | ≤25 | 0.075-0.4 | 245 | 59 |
Ф2400×4500 | 33 | ≤25 | 0.074-0.4 | 380 | 65 |
Ф2700×3600 | 39 | ≤25 | 0.074-0.4 | 400 | 91.3 |
Ф2700×4000 | 40 | ≤25 | 0.074-0.4 | 400 | 94 |
Ф2700×4500 | 48 | ≤25 | 0.074-0.4 | 430 | 102 |
Ф3200×4500 | 65 | ≤25 | 0.075-0.4 | 800 | 137 |
Ф3600×4500 | 90 | ≤25 | 0.074-0.4 | 850 | 158 |
Ф3600×6000 | 110 | ≤25 | 0.074-0.4 | 1250 | 175 |
Ф3600×8500 | 131 | ≤25 | 0.074-0.4 | 1800 | 252 |
Ф4000×5000 | 121 | ≤25 | 0.074-0.4 | 1500 | 203 |
Ф4000×6000 | 146 | ≤25 | 0.074-0.4 | 1600 | 218 |